Suspended Solids Monitor Used in a Paper Mill
Solids measurement in the paper and pulp industry has traditionally been difficult with variable solids loads, variable colours and variable particle size distribution. The SoliSense® from Pi, suspended solids monitor, provides a reliable and maintenance free solution.
A CRONOS® SoliSense® unit was purchased by Northwood Tissue in 2018. Manufacturing over 160 million toilet rolls per year, Northwood Tissue is a leading provider of high-quality wiping and paper hygiene products.
Paper mills require substantial amounts of water for the paper making process, and so most mills aim to recycle as much of the water used as possible. This is known as ‘closing the loop’. After the pulping process is complete, a ‘thick stock’ is produced. This is a mixture of water and the suspended solids that go to make paper, such as cellulose fibres and fillers. The thick stock is then diluted down to ‘thin stock’ (approximately 1% suspended solids). The thin stock is transported onto the ‘wire’, a mesh that collects the solids as this is what is turned into paper. The excess water from the thin stock drains through the mesh and is collected in a large tank. This water is referred to as ‘white water’ due to its colour. The amount of suspended solids in the white water is monitored as part of the water treatment regime.
The SoliSense® from Pi can measure suspended solids from 2 NTU all the way up to >8%. It is stable, reliable and suitable for all potable, waste and process waters. Not only that, the SoliSense® can go up to 12 months between calibration and maintenance, maximising process uptime and minimising costs. It is also available with an ‘AutoClean’ function that allows the suspended solids sensor to automatically flush the optical window with a jet of clean water at predefined intervals to avoid sensor fouling.
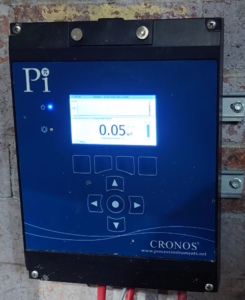
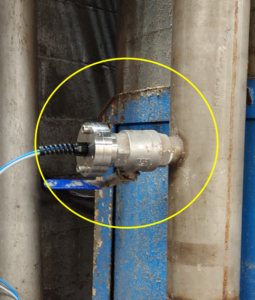
The SoliSense® can be fitted in a variety of ways such as on the end of a pole for dip mounting into a tank or channel, flow cells for at-line measurement, and as in this application, pipe insertion for in-line measurements. Pipe insertion uses a valve which allows for retraction and removal of the sensor without shutting down the process. Therefore, when Pi’s service engineers attended Northwood’s site to service and calibrate this system, process downtime was not an issue. This means that the process continued to run as normal, saving time and money.
To learn more about the technology that drives the SoliSense®, please click here. To discuss your application with one of our experts, give us a ring on 01282 422835.